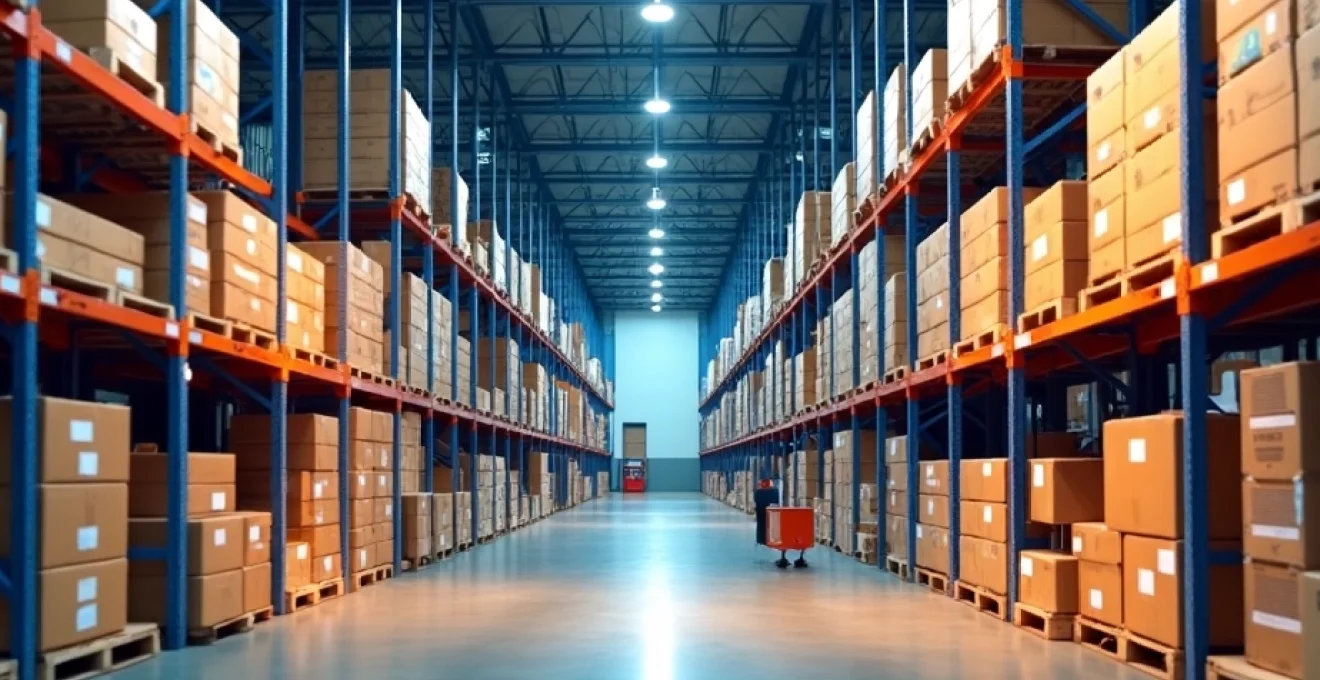
Effective warehouse inventory management is crucial for businesses to maintain optimal stock levels, reduce costs, and improve operational efficiency. As supply chains become increasingly complex, implementing best practices in inventory control can make the difference between a thriving operation and one that struggles with inefficiencies. From leveraging advanced technologies to adopting strategic methodologies, there are numerous approaches to enhance warehouse inventory management. This comprehensive guide explores key strategies and techniques that can help organizations streamline their inventory processes and maximize productivity.
Warehouse management systems (WMS) for inventory control
Implementing a robust Warehouse Management System (WMS) is fundamental to achieving effective inventory control. A WMS provides real-time visibility into stock levels, locations, and movements, enabling warehouse managers to make informed decisions quickly. These systems can automate many aspects of inventory management, from receiving and putaway to picking and shipping, significantly reducing manual errors and improving overall accuracy.
Modern WMS solutions often integrate with other business systems, such as Enterprise Resource Planning (ERP) software, to provide a holistic view of the supply chain. This integration allows for better demand forecasting, inventory optimization, and order fulfillment. Additionally, many WMS platforms now offer mobile capabilities, allowing warehouse staff to access and update inventory information on the go using handheld devices or tablets.
One of the key benefits of a WMS is its ability to optimize warehouse space utilization. By analyzing historical data and current inventory levels, these systems can suggest the most efficient storage locations for items based on factors such as size, weight, and frequency of access. This optimization can lead to significant improvements in warehouse layout and reduce picking times substantially.
ABC analysis and cycle counting methodologies
ABC analysis is a critical inventory categorization method that allows warehouse managers to prioritize their inventory control efforts. This approach is based on the Pareto principle, which suggests that a small percentage of items often account for a large portion of the value in a system. By implementing ABC analysis, businesses can focus their resources on managing the most valuable or critical items in their inventory.
Implementing pareto principle in inventory classification
In ABC analysis, inventory items are typically classified into three categories:
- A items: High-value products that require close monitoring and frequent counting
- B items: Moderate-value products that need regular, but less frequent attention
- C items: Low-value products that can be managed with minimal oversight
This classification allows warehouse managers to allocate their time and resources more effectively, ensuring that high-value items receive the most attention while still maintaining adequate control over lower-value inventory.
Frequency-based cycle counting techniques
Cycle counting is a continuous inventory auditing method that involves counting a small subset of inventory on a regular basis, rather than conducting a full physical inventory count annually. This approach provides several advantages, including more accurate inventory records, reduced disruption to daily operations, and the ability to identify and address discrepancies quickly.
When implementing cycle counting, it's essential to establish a schedule that aligns with the ABC classification. For example:
- A items: Counted monthly or even weekly
- B items: Counted quarterly
- C items: Counted semi-annually or annually
By focusing on high-value items more frequently, businesses can maintain tighter control over their most critical inventory while still ensuring accuracy across all stock levels.
Integration of RFID technology in cycle counting
Radio Frequency Identification (RFID) technology has revolutionized the cycle counting process in many warehouses. RFID tags attached to inventory items can be scanned quickly and accurately, eliminating the need for manual counting in many cases. This technology not only speeds up the cycle counting process but also reduces human error and provides real-time inventory updates.
Implementing RFID for cycle counting can lead to significant time savings and improved accuracy. For instance, a warehouse that previously required several days to complete a full inventory count might now be able to perform the same task in a matter of hours using RFID technology.
Statistical sampling methods for large inventories
For warehouses with extensive inventories, statistical sampling methods can be employed to estimate overall inventory accuracy without the need to count every item. These methods involve selecting a representative sample of items to count and using statistical analysis to extrapolate the results to the entire inventory population.
While statistical sampling doesn't provide the same level of accuracy as a complete count, it can be a valuable tool for identifying trends and potential issues in inventory management. It's particularly useful for C items, where the cost of frequent full counts may outweigh the benefits.
Just-in-time (JIT) inventory strategies for warehouses
Just-in-Time (JIT) inventory management is a strategy aimed at reducing inventory holding costs by receiving goods only as they are needed in the production process. While traditionally associated with manufacturing, JIT principles can be adapted for warehouse operations to improve efficiency and reduce carrying costs.
Kanban systems in warehouse inventory management
Kanban is a visual system for managing work as it moves through a process, originally developed as part of Toyota's lean manufacturing practices. In warehouse inventory management, Kanban can be used to signal when it's time to replenish stock, ensuring that inventory levels are maintained at optimal levels without excess.
Implementing a Kanban system in a warehouse might involve using physical cards or digital signals to indicate when stock levels reach a predetermined reorder point. This visual cue triggers the replenishment process, helping to prevent stockouts while minimizing excess inventory.
Pull-based replenishment models
Pull-based replenishment is a core concept in JIT inventory management. In this model, inventory is "pulled" through the supply chain based on actual customer demand rather than being "pushed" based on forecasts. For warehouses, this means closely aligning inventory levels with customer orders and replenishing stock only as needed.
Implementing a pull-based system requires close coordination with suppliers and a deep understanding of demand patterns. It often involves setting up vendor-managed inventory (VMI) arrangements or consignment stock agreements to ensure rapid replenishment when needed.
Supplier relationship management for JIT success
Successful implementation of JIT inventory strategies in warehouses heavily depends on strong supplier relationships. Warehouses need to work closely with suppliers to ensure they can deliver small quantities of inventory quickly and reliably. This often involves:
- Establishing clear communication channels
- Sharing demand forecasts and real-time inventory data
- Developing contingency plans for supply disruptions
- Negotiating flexible delivery terms
By fostering strong supplier partnerships, warehouses can reduce lead times, improve inventory accuracy, and respond more quickly to changes in demand.
Advanced forecasting techniques for inventory planning
Accurate demand forecasting is crucial for effective inventory management. Advanced forecasting techniques leverage historical data, market trends, and machine learning algorithms to predict future demand with greater precision. These methods help warehouses maintain optimal inventory levels, reducing both stockouts and excess inventory.
One of the most promising developments in this area is the use of artificial intelligence (AI) and machine learning for demand forecasting. These technologies can analyze vast amounts of data, including seasonal trends, economic indicators, and even social media sentiment, to generate more accurate predictions.
For example, a warehouse might use AI-powered forecasting to:
- Predict seasonal demand fluctuations with greater accuracy
- Identify emerging trends in customer buying patterns
- Adjust inventory levels in real-time based on market conditions
- Optimize safety stock levels to balance cost and service levels
By incorporating these advanced forecasting techniques, warehouses can significantly improve their inventory planning and reduce the costs associated with overstocking or stockouts.
Warehouse layout optimization for inventory efficiency
The physical layout of a warehouse plays a crucial role in inventory management efficiency. A well-designed layout can significantly reduce picking times, improve accuracy, and increase overall productivity. Optimizing warehouse layout involves considering factors such as product characteristics, order patterns, and storage equipment.
Slotting strategies and product velocity analysis
Slotting is the process of determining the most efficient placement of products within a warehouse. Effective slotting strategies take into account factors such as product velocity (how quickly items move through the warehouse), size, weight, and any special storage requirements.
Product velocity analysis involves categorizing items based on how frequently they are picked. Fast-moving items should be placed in easily accessible locations, typically at waist height and near the packing and shipping areas. This approach minimizes travel time for pickers and improves order fulfillment speed.
Cross-docking implementation for Fast-Moving items
Cross-docking is a logistics practice where products are unloaded from incoming trucks and loaded directly onto outbound trucks with minimal or no storage in between. This technique is particularly useful for fast-moving items or pre-sold merchandise.
Implementing cross-docking can significantly reduce handling costs and storage requirements. It's especially effective for perishable goods or items with high demand volatility. By designating specific areas for cross-docking operations, warehouses can streamline the flow of these high-velocity products and reduce overall inventory holding costs.
Zone picking and wave picking methodologies
Zone picking and wave picking are two popular methodologies for improving picking efficiency in warehouses. In zone picking, the warehouse is divided into zones, with each picker responsible for picking items from their assigned zone. This method reduces travel time and congestion in the warehouse.
Wave picking, on the other hand, involves releasing a group of orders to be picked simultaneously. This method allows for better workload balancing and can be particularly effective when combined with automated sorting systems.
Both methods can significantly improve picking efficiency, but the choice between them depends on factors such as warehouse size, product mix, and order characteristics.
Ergonomic considerations in inventory placement
Ergonomics plays a crucial role in warehouse layout optimization. Proper ergonomic design can reduce worker fatigue, improve productivity, and decrease the risk of injuries. When it comes to inventory placement, ergonomic considerations include:
- Placing frequently picked items at waist height to reduce bending and reaching
- Using adjustable shelving to accommodate products of different sizes
- Implementing lift-assist devices for heavy items
- Ensuring adequate lighting in all storage areas
By incorporating ergonomic principles into inventory placement strategies, warehouses can create a safer, more efficient working environment for their employees.
Key performance indicators (KPIs) for inventory management
Measuring and monitoring Key Performance Indicators (KPIs) is essential for assessing the effectiveness of inventory management practices and identifying areas for improvement. Some critical KPIs for warehouse inventory management include:
- Inventory Turnover Ratio: Measures how many times inventory is sold and replaced over a period
- Carrying Cost of Inventory: The total cost of holding inventory, including storage, insurance, and depreciation
- Order Picking Accuracy: The percentage of orders picked correctly
- Fill Rate: The percentage of customer orders that can be fulfilled from available stock
- Days Sales of Inventory (DSI): The average number of days it takes to sell inventory
Regularly tracking these KPIs allows warehouse managers to identify trends, set benchmarks, and make data-driven decisions to optimize inventory management processes. It's important to establish clear targets for each KPI and regularly review performance against these targets.
Advanced analytics tools can help in visualizing KPI data and uncovering insights that might not be immediately apparent. For example, analyzing the relationship between inventory turnover and fill rates can help in finding the optimal balance between inventory levels and customer service.
By implementing these best practices in warehouse inventory management, businesses can significantly improve their operational efficiency, reduce costs, and enhance customer satisfaction. From leveraging advanced technologies like WMS and RFID to implementing strategic methodologies such as ABC analysis and JIT inventory, there are numerous approaches to optimizing inventory control. The key is to continually assess and refine these practices to adapt to changing market conditions and business needs.